Some Of Alcast Company
Some Of Alcast Company
Blog Article
Alcast Company Can Be Fun For Anyone
Table of ContentsRumored Buzz on Alcast CompanyAlcast Company - TruthsSome Known Incorrect Statements About Alcast Company Alcast Company Fundamentals ExplainedGetting My Alcast Company To WorkUnknown Facts About Alcast Company
Chemical Comparison of Cast Aluminum Alloys Silicon promotes castability by minimizing the alloy's melting temperature and improving fluidity during casting. Additionally, silicon contributes to the alloy's stamina and use resistance, making it useful in applications where durability is essential, such as automobile parts and engine components.It additionally enhances the machinability of the alloy, making it less complicated to refine right into completed products. In this way, iron adds to the total workability of aluminum alloys.
Manganese adds to the strength of light weight aluminum alloys and boosts workability. Magnesium is a lightweight aspect that supplies strength and impact resistance to aluminum alloys.
Some Ideas on Alcast Company You Should Know
Zinc enhances the castability of aluminum alloys and helps regulate the solidification process throughout casting. It boosts the alloy's strength and firmness.

The key thermal conductivity, tensile stamina, yield toughness, and elongation differ. Select ideal raw products according to the performance of the target item generated. Amongst the above alloys, A356 has the highest possible thermal conductivity, and A380 and ADC12 have the most affordable. The tensile restriction is the opposite. A360 has the very best yield toughness and the highest elongation rate.
The 8-Second Trick For Alcast Company
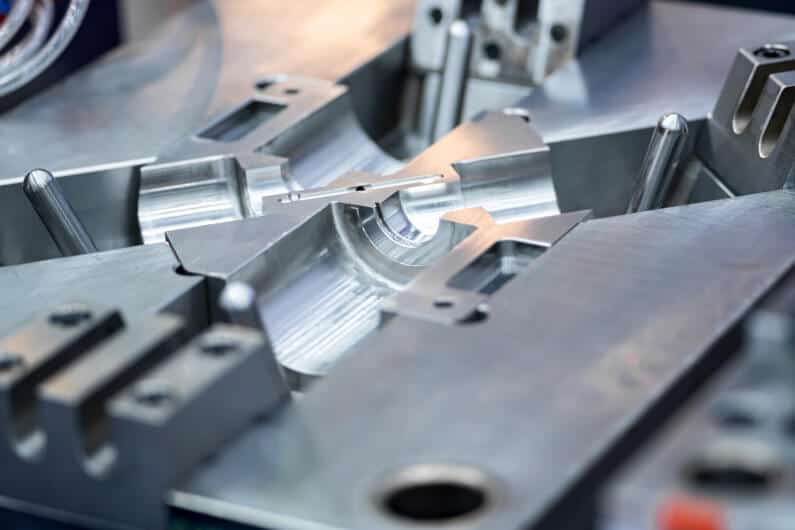
In precision casting, 6063 is appropriate for applications where complex geometries and high-quality surface area finishes are paramount. Examples consist of telecommunication units, where the alloy's exceptional formability permits for sleek and visually pleasing styles while keeping structural stability. In the Illumination Solutions market, precision-cast 6063 parts develop classy and efficient illumination fixtures that need detailed forms and good thermal efficiency.
It results in a finer surface finish and much better deterioration resistance in A360. In addition, the A360 exhibits superior elongation, making it optimal for complicated and thin-walled elements. In accuracy casting applications, A360 is appropriate for markets such as Consumer Electronics, Telecommunication, and Power Devices. Its boosted fluidity allows for elaborate, high-precision parts like smart device coverings and interaction gadget housings.
The Main Principles Of Alcast Company
Its distinct buildings make A360 a beneficial option for accuracy spreading in these industries, improving item durability and top quality. Light weight aluminum alloy 380, or A380, is an extensively made use of casting alloy with numerous distinct qualities. It uses excellent castability, making it an optimal selection for precision casting. A380 displays great fluidness when molten, ensuring complex and detailed mold and mildews are properly duplicated.
In precision spreading, light weight aluminum 413 radiates in the Customer Electronic Devices and Power Tools sectors. This alloy's remarkable rust resistance makes it an excellent selection for outside applications, guaranteeing long-lasting, long lasting products in the stated markets.
See This Report about Alcast Company
When you have chosen that the aluminum die casting process appropriates for your task, an important next step is selecting the most proper alloy. The light weight aluminum alloy you choose will significantly influence both the casting process and the homes of the end product. Due to this, you should make your choice very carefully and take an informed technique.
Establishing the website link most ideal light weight aluminum alloy for your application will mean considering a vast variety of attributes. The first category addresses alloy features that impact the manufacturing procedure.
The Single Strategy To Use For Alcast Company
The alloy you select for die spreading directly impacts several elements of the spreading process, like exactly how easy the alloy is to deal with and if it is vulnerable to casting issues. Hot cracking, also called solidification splitting, is a common die spreading defect for light weight aluminum alloys that can cause internal or surface-level splits or splits.
Certain light weight aluminum alloys are more vulnerable to warm cracking than others, and your choice must consider this. Another common flaw discovered in the die spreading of light weight aluminum is die soldering, which is when the cast adheres to the die walls and makes ejection tough. It can harm both the actors and the die, so you should search for alloys with high anti-soldering residential properties.
Deterioration resistance, which is currently a notable characteristic of aluminum, can vary considerably from alloy to alloy and is a necessary particular to think about relying on the ecological problems your product will be exposed to (aluminum metal casting). Put on resistance is an additional home typically sought in light weight aluminum products and can distinguish some alloys
Report this page